Information on custom molded parts
Élastomont offers a full line of molded rubber parts. Our engineering department can analyze your piece to improve it for resistance to higher temporal wear. In addition, our engineering department can reproduce an existing or new part from a sample, a technical drawing in harmony with the environment of the room (abrasion, chemical resistance, environmental resistance). Our expertise gained over time will allow you to significantly reduce your production costs.
We offer several types of castings such as: compression molding, transfer molding and injection molding. Élastomont can manufacture rubber parts molded with different formulas such as: Neoprene, Styrene-Butadiene, HNBR, XNBR, Silicone, EPDM, Hypalon, Natural Rubber, Butyl, Nitrile (Buna-N), fluorosilicone, polyurethane, Viton, SBR, SMP 800C. We also work with the following specifications: FDA/NSF, RoHS, UL, USP, Class VI, ASTM, MIL Specs.
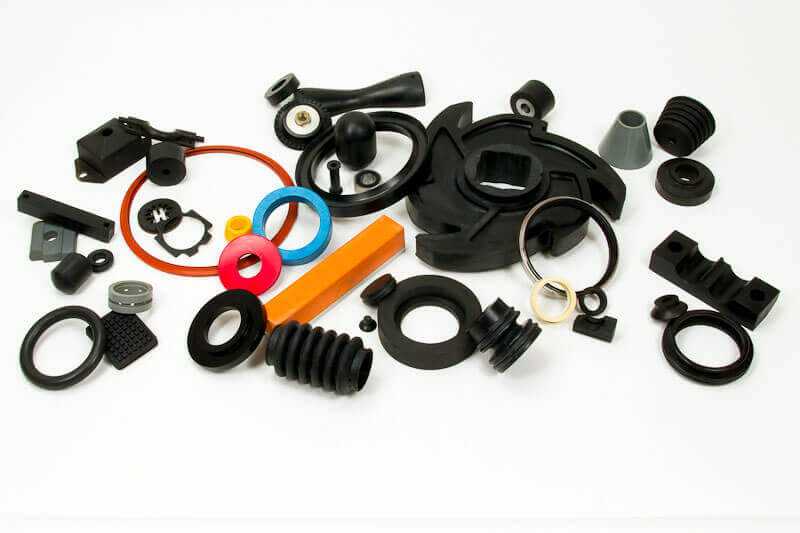
List of rubber
Neoprene rubber molded parts
Pros:
- Inherent flame resistance;
- Moderate oil and gasoline resistance;
- Excellent adhesion to fabrics and metals;
- Very good resistance to weathering, the ozone and natural aging;
- Good resistance to abrasions and cracks caused by flexing;
- Very good resistance to alkalis and acids.
Cons:
- Poor resistance to aromatic and oxygenated solvents;
- Limited use at low temperatures.
Applications:
When light oil resistance and weather resistance are both necessary (sealing washers and gaskets, sealing for doors and windows, pipe for steam, gardening or radiators, wires and cables).
Neoprene rubber datasheet
Styrene rubber-butadienes molded parts
Pros:
- Excellent impact resistance;
- Very good resilience;
- Resistance to abrasion and elasticity;
- Low temperature flexibility.
Cons:
- Poor resistance to aromatic and oxygenated solvents;
- Limited use at low temperatures;
Applications:
Non-critical, high-volume (sealing washers and gaskets, hoses, rubber skirts, Grade II industrial belts).
Syrene rubber-butadienes datasheet
HNBR (hydrogenated nitrile) molded parts
Pros:
- High resistance to additives in technical oils;
- Low vapor and gas permeability;
- Good resistance to low temperatures down to -30 °C, depending on the type used;
- Good ozone resistance and high wear resistance;
- Heat resistant up to 150 °C.
HNBR rubber datasheet
XNBR (carboxylated nitrile) molded parts
The carboxylated nitrile rubbers (XNBR) are improved NBR versions that combine the technical properties of the nitrile rubber (NBR) with wear resistance improved versions. It is mainly used for gaskets for heavy industrial applications.
Pros:
- High thermal resistance;
- Good non-stick properties;
- Excellent chemical resistance;
- Good UV resistance;
Cons:
- Low tensile strength;
- Low abrasion resistance;
- Difficult to stick.
Applications:
- Food industry;
- Industrial Maintenance (high temperatures);
- Seals.
XNBR rubber datasheet
Silicon molded parts
The silicone rubber is physiologically inert, allowing its use in a wide range of applications, particularly in the medical sector. It is also very stable in hostile environments; its operating properties remain invariable over a wide range of temperatures.
Pros:
- High thermal resistance;
- Good non-stick properties;
- Excellent chemical resistance;
- Good UV resistance;
Cons:
- Low tensile strength;
- Low abrasion resistance;
- Difficult to stick.
Applications:
- Food industry;
- Industrial Maintenance (high temperatures);
- Seals.
Silicon rubber datasheet
Rubber ethylene propylene diene molded parts
Pros:
- Excellent resistance to heat, the ozone and sunlight;
- Very good low temperature flexibility;
- Good resistance to alkalis, acids, oxygenated solvents, water and steam;
- Excellent color stability.
Cons:
- Low resistance to oil, gasoline and solvents;
- Poor adhesion to fabrics and metals.
Applications:
- Seals for doors and windows;
- Seals for the automotive sector;
- Gaskets and washers for electrical equipment;
- Conveyor belts;
- Steam hoses;
- Gardening or for radiators;
- Caulking material.
Hypalon molded parts
Pros:
- Excellent resistance to oxidation and weathering, the ozone and hydrocarbon solvents;
- Good fire resistance;
- It is self-extinguishing;
- Resistant to most inorganic chemicals except chlorine, strong acids and oxidants.
Cons:
- Average resistance to aliphatic and aromatic hydrocarbons.
Applications:
- Antacid coatings, cable sheathing;
- Flammable material when in contact with hot oil.
Natural rubber molded parts
Pros:
- Excellent tensile strength, tear and abrasion resistance;
- Excellent elasticity;
- Good flexibility at low temperatures;
- Good adhesion to fabrics and metals;
Cons:
- Low resistance to heat, the ozone and sunlight;
- Very little resistance to oil, gasoline and solvents.
Applications:
When the abrasion resistance and elasticity are critical (recovery of rails belts for low temperature applications, pipes, tank interior covers, cyclones, concentrators.)
Natural rubber datasheet
Butyl molded parts
Pros:
- Exceptional gas and vapor impermeability;
- Good resistance to heat, oxygen, the ozone and sunlight;
- High energy absorption (damping);
- Excellent resistance to alkalis and oxygenated solvents, water and steam;
- Good resistance to heat tearing.
Cons:
- Poor persistence under compression;
- Low resilience;
- Low resistance to oil and gasoline;
- Difficult application.
Applications:
- Gaskets and washers;
- Inner tubes for tires;
- Balloon interior coating;
- Pipes.
Nitrile molded parts
Pros:
- Very good resistance to oil and gasoline;
- Excellent resistance to hydraulic fluids petroleum-based;
- Good resistance to solvents;
- Very good resistance to alkalis and acids.
Cons:
- Poor resistance to the ozone, sunlight and natural aging;
- Poor resistance to aromatic and oxygenated solvents.
Applications:
When the oil resistance is the major concern (gaskets for machinery in contact with oil, grease and gasoline, white certified products for food contact, oil resistant belts, pipe coating, wires and cables).
Nitrile rubber datasheet
Fluorosilicone molded parts
Pros:
Good electrical properties is the excellent weather resistance and excellent resistance to the ozone and UV. Compared to standard silicone, fluorosilicones have significantly better chemical resistance to hydrocarbons, aromatic mineral oils and aromatic hydrocarbons with low molecular weight, such as benzene and toluene.
Cons:
- Low tensile strength and low resistance to tearing and abrasion.
Applications:
- Gasket fuel systems;
- Aerospace application, membranes;
- Seals.
Polyuréthane molded parts
Pros:
- Material with a wide range of hardness;
- Excellent mechanical properties, tear strength, abrasion resistance, resilience, bending, shock;
- Good resistance to oils, oil derivatives, water, impermeability to gases.
Cons:
- Not resistant to flame or chlorinated solvents.
Applications:
- Skates;
- Wipers;
- Stops;
- Shock absorbent;
- Shingles;
- Roll, idler roll, etc;
- All technical parts requiring high abrasion resistance.
Viton molded parts
Pros:
- Unparalleled resistance to heat, oxidation, the ozone and bad weather;
- Excellent resistance to a wide variety of fluids including alphatiques and aromatic hydrocarbons, halogenated fluids, strong acids;
- Excellent resistance to deformation under pressure, providing sealing performance and unmatched durability from any non-fluorinated elastomer.
Cons:
- Very high cost.
Applications:
- Automobiles;
- Aerospace;
- Gasoline;
- Lubricants;
- Chemical and energy procedures, gaskets.